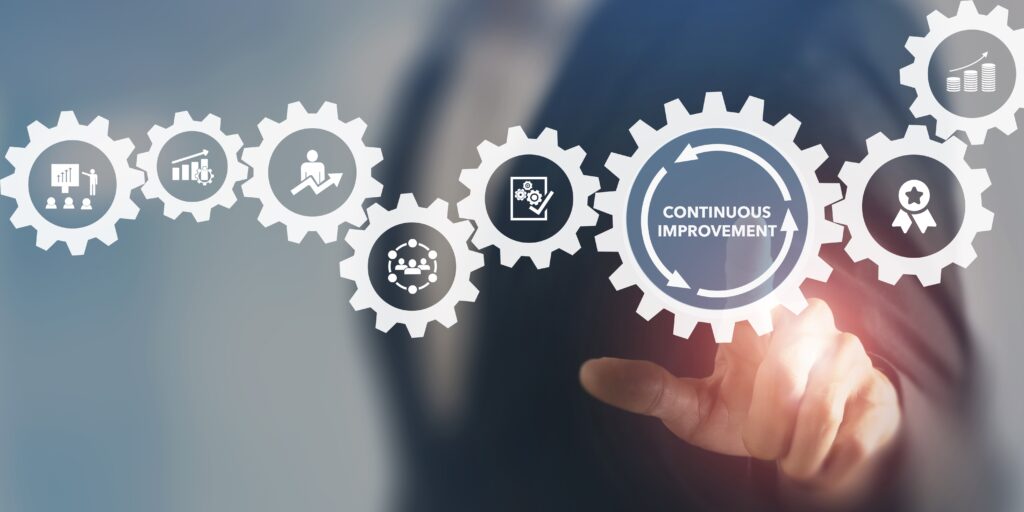
Continuity
Serving
Solutions
Various steps
We take various steps to ensure continuity of delivery:
1. Risk spreading and quality assurance
As a medium-sized company, we spread our production across different countries, factories and locations to effectively spread risks. We attach great importance to quality assurance and regularly carry out factory visits.
2. Flexibility in purchasing quantities
Compared to larger companies, we have the flexibility to adjust purchasing quantities, for example by changing container quantities, which gives us a competitive advantage.
3. Inventory flexibility
Part of our inventories are managed internally, making us exceptionally flexible in our supply chain. In case of significant growth in demand we offer air freight as an option, but always in consultation with the customer and with regular price revisions to compensate for the higher costs, taking into account sustainability considerations.
4. Strategic inventory strategy
Our inventory strategy is based on an average need of several months, with flexibility for exceptional situations. Our strong solvency enables us to quickly respond to changing demand patterns by immediately ordering, paying in advance and scaling up.
5. Accurate forecasting
To ensure that deliveries take place uninterrupted, Medica Europe maintains a safety stock for customer-specific end products. This inventory is accurately calculated based on your consumption patterns. In case of unexpected limitations in the availability of raw materials, Medica Europe can ensure that it is not completely dependent on one supplier, thanks to its diverse supplier network.
6. Continuous monitoring
Our purchasing department continuously monitors market developments at product locations and in transport through benchmarking. This way we remain proactive in ensuring an efficient and resilient supply chain.
Continuity
Various steps
We take various steps to ensure continuity of delivery:
1. Risk spreading and quality assurance
As a medium-sized company, we spread our production across different countries, factories and locations to effectively spread risks. We attach great importance to quality assurance and regularly carry out factory visits.
2. Flexibility in purchasing quantities
We have the flexibility to quickly adjust purchasing quantities, for example by changing container quantities, which gives us a competitive advantage.
3. Inventory flexibility
Our inventories are managed internally, making us exceptionally flexible in our supply chain. In case of significant growth in demand we offer air freight as an option, but always in consultation with the customer and with periodic price revisions to compensate for the higher costs, taking into account sustainability considerations.
4. Strategic inventory strategy
Our inventory strategy is based on an average need of several months, with flexibility in exceptional situations. Our strong solvency enables us to quickly respond to changing demand patterns by immediately ordering, paying in advance and scaling up.
5. Accurate forecasting
To ensure that deliveries take place uninterrupted, Medica Europe maintains a safety stock for customer-specific end products. This inventory is accurately calculated based on customer consumption patterns. In case of unexpected limitations in the availability of raw materials, Medica Europe can ensure that it is not completely dependent on one supplier, thanks to its diverse supplier network.
6. Continuous monitoring
Our purchasing department continuously monitors market developments at product locations and in transport through benchmarking. This way we remain proactive in ensuring an efficient and resilient supply chain.
Delivery takes place within 48 hours as standard. Our deliveries follow the ABC principle:
Day A - order received.
Day B - preparing order.
Day C - extradition.
In specific situations, variants (e.g. AAB) of this principle are possible.
At Medica Europe we strive to provide you with the best service, even in emergency situations. If your hospital urgently needs stock due to unforeseen circumstances, we are easily accessible. You can report the urgency via your contact person or our Customer Service department. The Purchasing & Logistics Manager and our logistics partner will then be informed. Once the goods have been collected, a truck is ready to deliver them to the desired location.
An average of several months applies to this. This depends on the component with the longest delivery time.
This involves a minimum period of a number of weeks and a maximum period of a number of months. This depends on the component with the longest delivery time.
We staan altijd klaar om samen met u te kijken naar de beste mogelijkheden en adviseren graag om tot de beste beslissing te komen voor uw specifieke situatie. Uw tevredenheid en efficiëntie zijn voor ons van het grootste belang.
Medica Europe uses procedures to prevent stock breakage. We periodically review the consumption figures in consultation with the customer and adjust our stock accordingly. We feed this data back to our planning department. If a stock shortage occurs due to unforeseen circumstances, we will contact you immediately to jointly determine the urgency of orders. We understand that the process in the hospital cannot come to a standstill and Medica Europe can guarantee delivery.
• A large economic stock on the trays.
• On average, a large number of months' stock of raw materials is unsterile. In emergencies, we can produce sterile products within a few weeks.
• A wide range of single-use products, so there is always a product that we can offer as an alternative.
Mission
Medica Europe positions itself as a leading player in the medical disposables industry, focused on relieving the burden on healthcare and delivering sustainable solutions. The pay-off ‘Serving Solutions’ serves as a guideline for all communication.
Make an appointment without obligation
Complete the form below
Or contact us on (0412) 67 13 00